- Swenson Walker Crystallizer Pdf Download
- Swenson Walker Crystallizer Pdf Editor
- Swenson Walker Crystallizer Pdf Filler
- Swenson Walker Crystallizer Pdf Reader
Outline of Report I. Crystallization: Definition and Industrial Importance II. Crystallization Equipment A. Tank and Batch-Type Crystallizers 1. Agitated Batch Crystallizer 2. Swenson-Walker Crystallizer 3. Wulff-Bock Crystallizer B. Evaporative Crystallizers C. Vacuum Crystallizers
Crystallization: Definition and Industrial Importance • It is a process whereby a solution is supersaturated so as to cause the formation of crystals. • It is the removal of a solute such as a salt from a solution by precipitating the solute from the solution.
• Crystallization is an important operation in the chemical industry as a method of purification and as a method of providing crystalline materials in the desired size range.
Crystallization Equipment • Crystallizing equipment can be classified according to the methods used to bring about supersaturation as follows:
1.
Tank and Batch-Type Crystallizers – supersaturation is produced by cooling the solution with negligible evaporation.
2.
Crystallizing Evaporators – supersaturation is produced by evaporation of the solvent with little or no cooling.
3.
Vacuum Crystallizers – supersaturation is produced by combined cooling and evaporation in an adiabatic evaporator.
Tank and Batch-Type Crystallizers • These are crystallizers which produce supersaturation by cooling.
• The material must have a solubility that varies greatly with temperature. • 3 types:
Agitated Batch Crystallizer
Tank and Batch-Type Crystallizers
SwensonWalker Crystallizer
Wulff-Bock Crystallizer
Agitated Batch Crystallizer • Water is circulated through the cooling coils and the solution is agitated by the propellers mounted on the central shaft. • See Figure 18-79, Perry’s HB, 8th ed.
Agitated Batch Crystallizer • FUNCTIONS OF THE AGITATOR 1. It increases the rate of heat transfer and keeps the temperature of the solution more uniform. 2. It also keeps the fine crystals in suspension, thus it gives them an opportunity to grow uniformly instead of forming large crystals or aggregates.
Agitated Batch Crystallizer • ADVANTAGES 1.
Production of more uniform crystals compared to older tanks.
2.
The crystals formed are very much finer than that from the older tanks.
•. DISADVANTAGES 1. It is a batch or discontinuous crystallizer. 2. The solubility is the least at the surface of the cooling coils. Therefore, crystal growth is most rapid at this point and the coils rapidly build up with a mass of crystals that decreases the rate of heat transfer.
Swenson-Walker Crystallizer • It consists of an open trough with a semicircular bottom having a cooling water jacket welded outside. • It is about 2 ft wide and 10 ft long. • The hot concentrated solution to be crystallized is fed at one end of the trough and cooling water usually flows through the jacket in counter current to the solution.
Swenson-Walker Crystallizer • A slow-speed spiral agitator, set as close as possible to the bottom of the trough, rotates and suspends the growing crystals on turning. • Blades pass close to the wall and break off any deposits of crystals on the cooled wall. • In order to control crystal size, it is sometimes desirable to introduce an extra amount of water into certain sections in the jacket. • A number of units may be joined together to give increased capacity.
Swenson-Walker Crystallizer • ADVANTAGES: 1. Large saving in floor space. 2. Large saving in material in process. 3. Saving in labor. 4. Free from inclusions and aggregations.
• DISADVANTAGES: 1. The product generally have a somewhat wide crystalsize distribution.
Wulff-Bock Crystallizer • It has similar characteristics as that of the SwensonWalker crystallizer, however, it depends on air cooling. • It consists of a shallow trough set inclined and mounted on rollers so that it can be rocked from side to side. • The slow rate of cooling in this crystallizer results in low capacity but it gives uniform crystals.
Wulff-Bock Crystallizer • ADVANTAGE: It gives more uniform crystals as compared to SwensonWalker Crystallizer.
•. DISADVANTAGE: The slow rate of cooling in this crystallizer results in low capacity.
Evaporative Crystallizers • These are crystallizers which produce supersaturation by evaporation of solvent. • The material must have a solubility that changes little with (or is independent of) temperature.
Vacuum Crystallizers • These are crystallizers which produce supersaturation by adiabatic evaporation with cooling. • The method of producing supersaturation in these crystallizers is the most important one for large-scale production. • Hot solution is introduced into a vacuum where the solvent evaporates and the solution is cooled adiabatically.
Forced Circulation Crystallizer • an 'active volume“ to get both required residence time for crystal growth and mother liquor desupersaturation • agitation rate • Control the extent of supersaturation arising from the evaporation, • Control the temperature difference in the heat exchanger
• a special design of the liquid-vapor separation area to avoid the formation of an excessive amount of fines, which is highly detrimental to crystal growth.
Forced Circulation Crystallizer • These systems can be either single or multiple effects. • Usually operate from low vacuum to atmosphere pressure. • Used for high evaporation rates and when crystal size is not of the utmost importance. • Almost any material of construction can be considered for the fabrication of these crystallizers. • Use vacuum cooling or evaporation method
Forced Circulation Crystallizer Typical products are: • NaCl (food or technical grade) • KNO3Na2 • SO4 • K2 SO4 • NH4Cl • Na2CO3H2O • Citric acid
Draft Tube Baffle (DTB) Crystallizer • AKA Messo-turbulence • Employ magma recirculation to control supersaturation generation • Use cooling, vacuum cooling and evaporation • The concept is such that if no (or little) heat make-up is required, it results in a rather compact arrangement; therefore the initial investment is minimized • operate with a rather low supersaturation so that very large coarse and uniform crystals can be produced only by providing extensive and costly dissolving of fines.
Draft Tube Baffle (DTB) Crystallizer • When destruction of fines not needed or wanted, baffles are omitted and the internal circulation rate is set to have the minimum nucleating influence on the suspension
Draft Tube Baffle (DTB) Crystallizer Typical products are: • boric acid • Na2SO4. 10H20 (Glauber salt) • melamine • citric acid • NaCIO3
Induced Circulation Crystallizer • provide additional agitation of the active volume of forced circulation crystallizers with the use of only one pump. • operates similarly to a Draft Tube Baffle crystallizer but without the internal agitation device • main applications are for evaporative crystallization cases • produce a narrow crystal size distribution • can be fabricated in almost any material of construction • limited to non-viscous solutions
Induced Circulation Crystallizer Typical products are: • NaCl • NH4ClO4 • NH4Cl
Surface-cooled (SC) Crystallizer • Same with surface-cooled-baffle (SCB) crystallizers • Use only surface cooling to generate supersaturation • Employ magma recirculation to control supersaturation generation • Do not provide mechanism for classified product removal • provide a mechanism for fines dissolution when baffle is present (SCB ONLY)
• The heat exchanger surface is the coldest part of the process and is prone to solids build-up so it is operated such that the tube-side and shell-side does not exceed 5-10°C
Oslo Type Crystallizer • AKA classified-suspension crystallizer • Oldest design for large, coarse crystals Design Criteria: • Employ liquor recirculation to control supersaturation generation • Use surface cooling, evaporation or adiabatic evaporative cooling to generate supersaturation • Provide a built-in mechanism for fines dissolution and classified product removal. • keeping most of the crystals in suspension without contact by a stirring device, thus enabling the production of large crystals of narrow size distribution
Oslo Type Crystallizer • classifying crystallization chamber is the lower part of the unit • upper part is the liquor-vapor separation area • Used for reactioncrystallization and separationcrystallization when several chemical species are involved.
Oslo Type Crystallizer
• Usually “close type” • the 'open' type is to be considered when very large settling areas are required or when the vessel must be fabricated out of high cost alloys or metals.
Oslo Type Crystallizer Typical products are: • (NH4)2 SO4 • Na2SO4 • AgNO3 • hydrated mono sodium glutamate • mono ammonium phosphate (MAP)
Crystallizer Configurations
Crystallizer Comparison Crystallizer Equipment
Rough Cost Estimate (1=highest)
Forced Circulation Crystallizer
4
Induced Circulation Crystallizer
2
Draft Tube Baffle (DTB) Crystallizer
1
Surface-cooled (SC) Crystallizer
5
Oslo Type Crystallizer
3
Crystallizer Equipment
Advantages
Disadvantage
Forced Circulation Crystallizer
• Least expensive type of crystallizer • Large range of sizes available • High rate of circulation reduces particle deposits on vessel walls
• Crystal size difficult to control
Draft Tube Baffle (DTB) Crystallizer
• Crystal size easy to control • Economic due to recyclability of fines • More energy efficient than forced-circulation crystallizers
• Frequent flushings required to minimize deposits on the crystallizer wall • Cannot effectively handle a high density slurry • Not easily reproduced in small scale
Surface-cooled (SC) Crystallizer
• Can handle high boiling point solution • Can handle solution that has such low temperature boiling point that evaporation by
Crystallizer Equipment
Advantages
Disadvantage
Oslo Type Crystallizer
• operating costs of the • Not easily reproduced Oslo type crystallizer in small scale unit are much lower than with any other type when both large and coarse crystals are required • Since crystals are not in contact with any agitation device, the amount of fines to be destroyed is lower and so is the corresponding energy requirement. • allows long cycles of production between washing periods.
Crystallization of Monosodium Glutamate
Crystallization of Monosodium Glutamate
Video • Forced Circulation Crystallizer
C:UsersChongDocumentsPARTECHCrystallizationgea-wiegand-anim
References • Samant, K.D. & O’Young, L. (2006). Understanding Crystallization and Crystallizer. Clearwaterbay Technology, Inc. • http://www.niroinc.com/evaporators_crystallizers/crystalliz ation.asp • http://www.alaquainc.com/Crystalizers.aspx • http://video.geap.com/video/852192/gea-wiegandanimation-forced • http://video.geap.com/channel/4103319/crystallization • http://www.slideshare.net/saravanamoorthy/crystallization
S E S N FORCED CIRCULATION CRYSTALLIZER W NQ Figure 5.2 Swenson forced-circulation crystallizer. FUNDAMENTALS magma, and if McCabe's AL law is applicable, a straight line plot of In n versus L will result. The intercept of this straight line with the size corresponding to L = 0 is the nuclei population density. Swenson Walker crystallizer is a continuous type crystallizer. This operation involves both heat and mass transfer. Crystallization is the formation of solid particles within a homogeneous phase. Its wide use has a two-fold basis; a crystal formed from an impure solution is itself pure.

Rigorous process development is critical to the success of the implementation of new production schemes. Swenson is a leader in the application of evaporation and crystallization processes for the production of a variety of chemicals. Our process engineers work closely with our clients to understand their needs and develop process designs that can effectively be implemented to achieve quality or recovery requirements.
Depending on the stage of the project, Swenson process development resources can support the client through the proof of concept to definitive feasibility study level.
For every installation, Swenson engineers combine their years of experience with proprietary design information, plant operating data, and state-of-the-art modeling software to develop innovative and dependable solutions for our clients.
Swenson has long recognized that the information available through testing is crucial to the success of the ultimate full-scale application and has maintained test facilities throughout our history.
Swenson Walker Crystallizer Pdf Download
The Swenson Test Center, located near Chicago in Harvey, Illinois, is equipped for laboratory analysis, bench-scale process development in glassware, and research and development as well as pilot scale operation. We can perform feasibility testing of virtually any product in either laboratory or pilot scale and have worked with more than 700 different compounds.
Swenson Walker Crystallizer Pdf Editor
Swenson uses internally developed design methods and software such as OLI to simulate complex aqueous chemistry. Running simulations helps to refine the process before the customer makes an investment in capital equipment.
Testing – Glassware
Data Exploration and Software Simulation
Glassware testing helps to provide proof of concept and to gather other necessary data such as yield, purity, loss on drying, and crystal morphology. Testing starts as a batch process and may be run as a continuous process when necessary. Data from glassware testing is used to further refine the process calculations.
Pilot Testing

Swenson Walker Crystallizer Pdf Filler
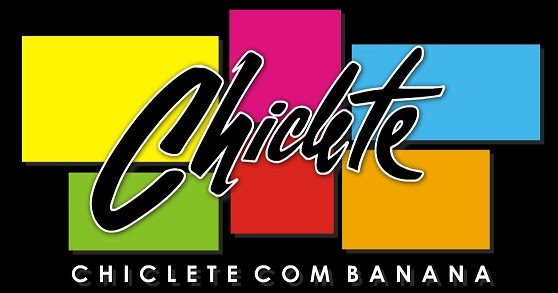
Swenson Walker Crystallizer Pdf Reader
Pilot testing is utilized to gather data necessary for plant design that cannot be acquired in glassware, such as crystal breakage, centrifuge data, and heater fouling. Pilot testing is usually done at 20 liter scale but also can be done at 1000 liter scale.
Process Design/Equipment Sizing
Swenson engineers utilize the data gathered from testing to design the most cost-effective system for the customer.
Benefits of Testing
The Test Center is equipped with everything necessary to turn a liquid feed into a dry solid. Operational tests are designed so that the test product will resemble the final product as closely as possible for customer evaluation.

Using these test results, Swenson engineers can assist customers in making knowledgeable decisions and recommend the appropriate equipment. Your solutions may be tested in these various models, the results compared, and the best design offered for the required product characteristics.
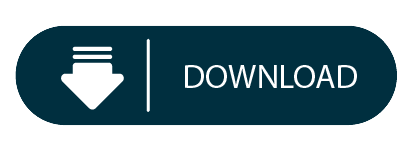